Is your commercial fleet facing operational efficiency challenges? Poorly chosen truck accessories can lead to increased downtime, higher fuel consumption, and escalating maintenance costs. The right accessories not only solve these problems but significantly enhance fleet performance and return on investment. As a leader in the truck accessories industry, we’ve witnessed how appropriate accessories can save commercial fleets up to 30% in operational costs.
1. Why Do Commercial Fleets Need Specialized Truck Accessories?
Standard truck configurations often fail to meet industry-specific needs. Did you know? Specialized accessories can directly impact your bottom line. Commercial fleets face unique challenges, from harsh weather conditions to special cargo requirements, all demanding customized solutions.
Regular accessories quickly fail in commercial environments. Construction company trucks need tool boxes that can withstand frequent loading of heavy materials, while logistics companies require solutions that resist vibrations from long-haul transportation. Professional accessories use stronger materials and designs built specifically for commercial use.
Custom truck accessories can significantly improve fleet efficiency. By optimizing storage space, reducing vehicle weight, and streamlining daily operations, these accessories translate directly into cost savings. For example, a mid-sized logistics company saved approximately 12% in fuel costs per vehicle annually after installing aluminum tool boxes and bodies.
Industry | Common Challenges | Recommended Specialized Accessories | Efficiency Improvement |
---|---|---|---|
Construction | Heavy tool storage, harsh jobsite conditions | Reinforced tool boxes, heavy-duty bumpers | 15-20% |
Logistics | Long-haul transport, multiple loading/unloading | Lightweight aluminum bodies, organizational storage systems | 10-15% |
Utilities | Remote area operations, specialized equipment needs | Custom tool racks, reinforced bumpers | 18-25% |
Agriculture | Muddy environments, seasonal usage | Anti-corrosion storage, off-road bumpers | 12-18% |
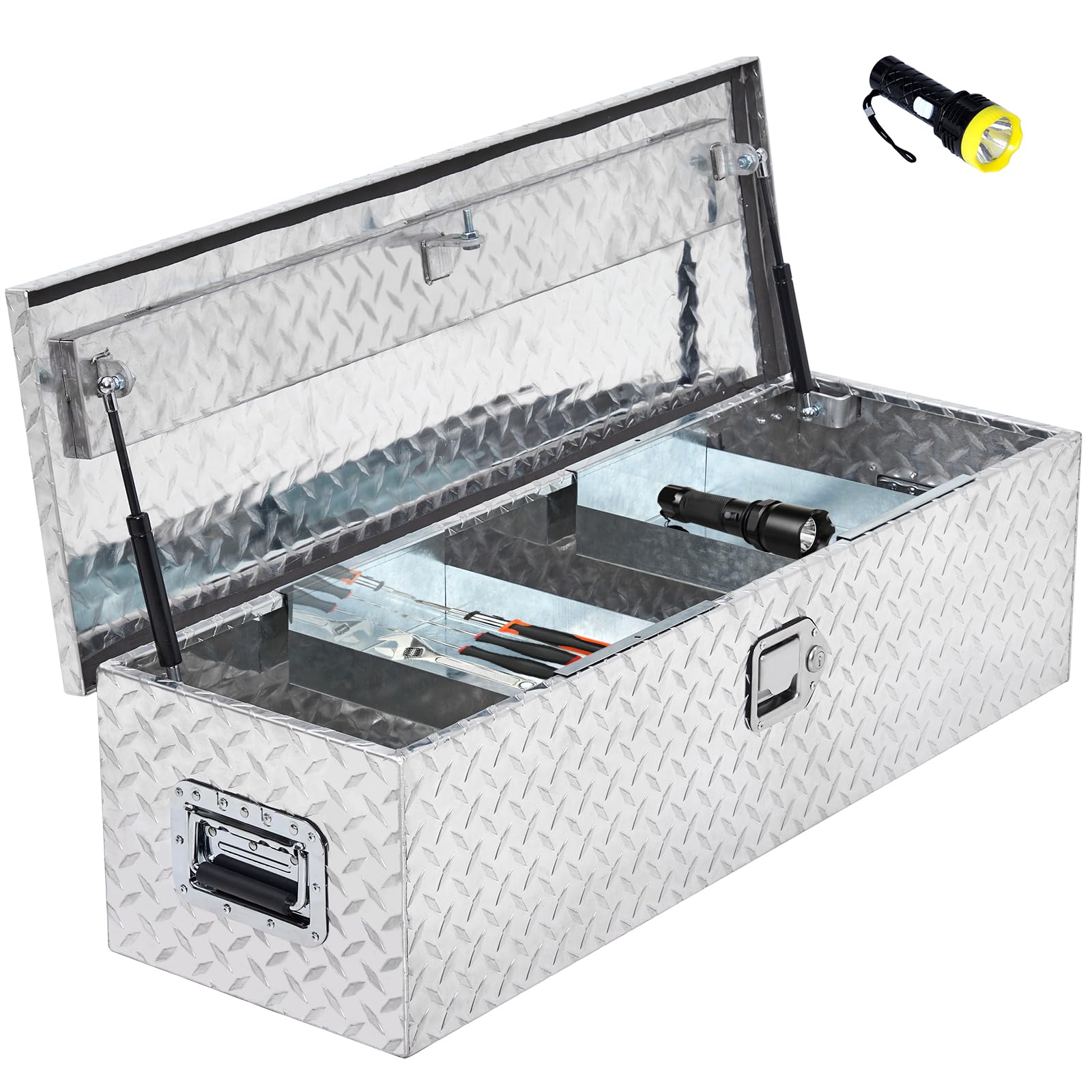
Specialized truck accessories have a direct impact on safety compliance. This is critical: The right accessories not only improve efficiency but also ensure compliance with industry safety standards. Many industries have strict equipment safety regulations, and professional accessories are typically designed to meet or exceed these standards.
ROI analysis shows that while professional accessories have higher initial costs, long-term savings are substantial. According to a recent industry report by Grand View Research, the automotive aftermarket continues to grow as fleet operators recognize the value of quality accessories. A study of 200 commercial fleet vehicles found that those with professional accessories had average maintenance costs reduced by 22% and downtime decreased by 17%. These figures translate into thousands of dollars saved per vehicle over a 5-year usage period.
2. What Makes Tool Boxes Essential Truck Accessories For Work Trucks?
Tool boxes are among the most fundamental and important accessories for work trucks. Let’s face it: Without proper tool storage solutions, work efficiency drops dramatically. Lost, damaged, or hard-to-find tools lead to project delays and increased costs.
Different types of accessories offer unique advantages. Side-mounted tool boxes provide convenient access without taking up bed space; underbody tool boxes utilize otherwise unused space beneath the vehicle; while topside tool boxes maximize storage capacity. Each type suits specific usage scenarios.
Tool Box Type | Best Use Case | Primary Advantages | Capacity Range |
---|---|---|---|
Side-mounted | Service vehicles needing frequent tool access | Convenient access, no reduction in bed space | 3-8 cubic feet |
Underbody | Vehicles with limited space but needing extra storage | Utilizes unused space, doesn’t affect vehicle appearance | 2-5 cubic feet |
Topside | Work trucks needing large capacity storage | Maximum storage space, complete protection | 5-12 cubic feet |
Combination | Multi-function work requirements | Flexible storage options, customized organization | 8-20 cubic feet |
Material choice is crucial for truck accessories performance. Aluminum tool boxes are lightweight (about 50% lighter than steel) and corrosion-resistant but may not be as durable as steel. Steel tool boxes offer maximum strength but are prone to rust and heavier. Composite materials provide good weather resistance but may not match metal options in extreme conditions.
This is worth noting: Security features are a key consideration when choosing truck accessories. Quality tool boxes should include tamper-resistant locks, reinforced hinges, and weather-tight seals. Some advanced models also offer integrated alarm systems or remote monitoring capabilities, particularly suitable for fleets storing high-value tools and equipment.
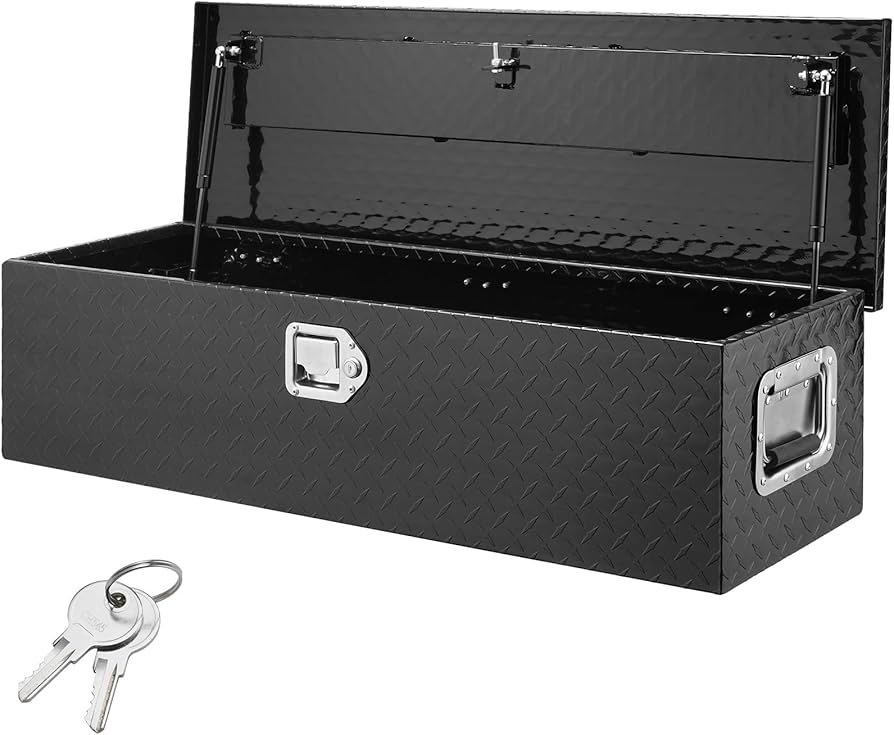
Choosing the right accessory size and configuration for industry needs is essential. Electricians might need long, narrow tool boxes with small compartments, while construction contractors require deep boxes that can accommodate large power tools. Many manufacturers offer customization options, including adjustable dividers, dedicated tool racks, and organizational systems.
One electrical company reported a 23% increase in technician efficiency after installing custom accessories in their service fleet, primarily due to improved tool organization and access convenience. This translated to nearly 45 minutes saved per vehicle per day, significantly increasing service call completion rates.
3. How Do Custom Bumpers Enhance Truck Performance?
Custom bumpers are far more than aesthetic upgrades. You might be surprised: They’re key components for improving fleet safety and performance. Standard bumpers are typically designed for light impacts, while commercial environments demand more robust solutions.
The impact resistance performance of truck accessories directly affects vehicle and driver safety. Quality custom bumpers are manufactured using thick steel plate or aluminum alloys capable of withstanding significantly greater impact forces. Many designs also include crash bars and reinforcement points for further protection.
Bumper Type | Material | Primary Functions | Suitable Environments |
---|---|---|---|
Standard Heavy-Duty | Steel (3/16″-1/4″ thick) | Basic collision protection, winch mounting | General commercial use |
Off-Road Reinforced | Steel (1/4″-3/8″ thick) | Enhanced obstacle protection, multiple mounting points | Construction, mining, forestry |
Lightweight High-Strength | Aluminum alloy | Reduces front-end weight while maintaining protection | Long-haul transport, fuel efficiency priority |
Multi-Function Integrated | Steel/aluminum hybrid | Integrated storage, lighting, and auxiliary equipment | Utilities, emergency services |
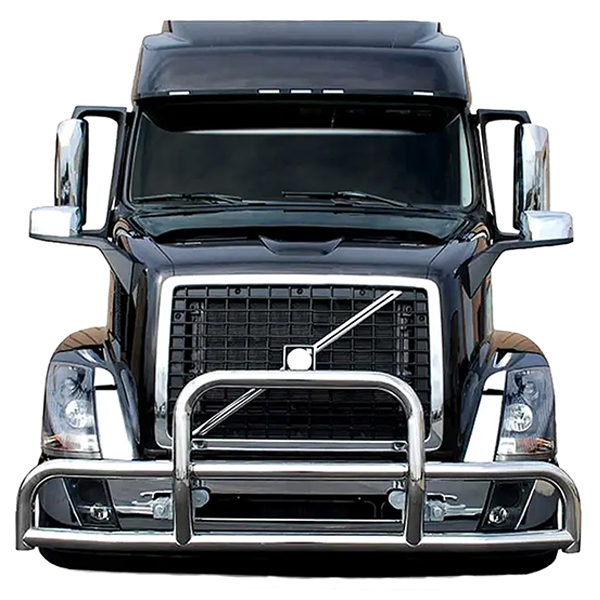
Additional functions provided by custom accessories significantly enhance work capabilities. Here’s the key point: Winch mounting points, integrated LED work lights, and auxiliary equipment mounting options translate into real-world work efficiency. For example, bumpers with integrated LED lighting can improve nighttime work area illumination by over 200%, enhancing safety and extending working hours.
Material durability directly impacts maintenance costs of truck accessories. Powder-coated steel bumpers offer excellent durability but require periodic inspection and rust prevention treatment. Aluminum options, while initially more expensive, are virtually maintenance-free and may prove more economical in the long run. A mid-sized construction company reported a 62% reduction in 5-year maintenance costs after switching to high-quality aluminum accessories.
Industry cases prove the value of custom truck accessories. A forestry company installed reinforced front bumpers across their entire fleet and reduced front-end damage-related downtime by 78%. With daily downtime costs of approximately $1,200, this upgrade paid for itself in less than a year.
4. What Benefits Do Aluminum Truck Bodies Provide?
Aluminum bodies are rapidly becoming the preferred choice for commercial fleets seeking efficient truck accessories. This fact stands out: Aluminum weighs approximately 40-60% less than traditional steel while maintaining excellent strength. This weight difference translates directly into significant fuel efficiency improvements.
The relationship between weight and fuel efficiency cannot be overlooked when selecting accessories. Research indicates that for every 10% reduction in vehicle weight, fuel efficiency improves by 6-8%. For commercial fleets traveling tens of thousands of miles annually, this can translate into thousands of dollars in fuel cost savings per vehicle per year.
Body Material | Weight Comparison | Fuel Efficiency Impact | Payload Capacity Impact |
---|---|---|---|
Traditional Steel | Baseline | Baseline | Baseline |
Aluminum | 40-60% lighter | 6-8% improvement | 15-20% increase |
Composite Materials | 30-45% lighter | 5-7% improvement | 10-15% increase |
Steel-Aluminum Hybrid | 20-30% lighter | 3-5% improvement | 8-12% increase |
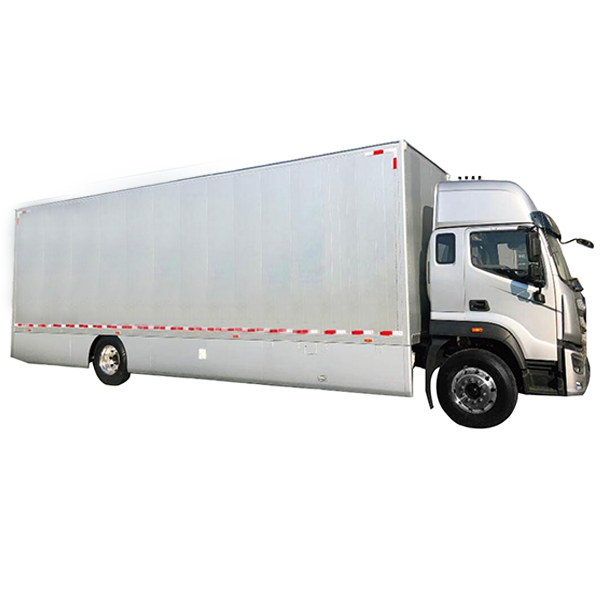
Corrosion resistance is one of aluminum’s primary advantages as a truck accessory. This is important: Unlike steel, aluminum doesn’t rust, maintaining its integrity even in harsh weather and road salt environments. This translates into longer service life and lower maintenance requirements. Many aluminum body manufacturers offer 10-15 year corrosion warranties, while steel bodies typically only have 3-5 years.
Modular design allows aluminum truck accessories to adapt to various industry needs. From service bodies with dedicated compartments to flatbed bodies with folding side panels, aluminum’s versatility makes it a multi-functional choice. This adaptability allows fleets to customize solutions to meet specific needs without sacrificing material benefits.
A distribution company that replaced their fleet’s steel bodies with aluminum accessories recorded the following results: 12% reduction in fuel consumption, 18% increase in payload capacity, and 34% lower maintenance costs over a 5-year period. According to The Business Research Company’s market report, the truck market continues to grow, indicating strong industry growth and increasing adoption of efficient accessories.
Long-term ownership cost analysis reveals the true value of aluminum truck accessories. While initial costs are 15-25% higher than steel, when considering fuel savings, reduced maintenance, and higher residual value, the total cost of ownership is typically lower within 3-5 years. Additionally, aluminum bodies typically last 40-60% longer than steel, further increasing long-term value.
5. How To Select The Right Truck Accessories For Your Fleet?
Choosing appropriate accessories requires a systematic approach. Let’s be clear: There’s no one-size-fits-all solution. Each fleet has unique needs depending on industry, operating environment, and specific challenges.
A framework for accessory selection based on industry-specific needs can simplify the decision process. Start by identifying core business functions, then assess current challenges and efficiency bottlenecks. This approach ensures accessory investments directly address real problems rather than just being “nice to have.”
Industry | Primary Operational Needs | Recommended Priority Accessories | Expected Efficiency Gains |
---|---|---|---|
Construction | Tool security, material transport, jobsite durability | Reinforced tool boxes, heavy-duty bumpers, anti-slip bed liners | 15-25% work efficiency improvement |
Delivery | Fuel efficiency, cargo security, quick access | Aluminum bodies, organizational systems, side-door storage | 12-18% operational cost reduction |
Utilities | Equipment organization, all-weather reliability, safety | Custom tool racks, all-weather storage, safety lighting | 20-30% service time reduction |
Landscaping | Versatility, clean separation, equipment security | Compartmentalized storage, water tank brackets, locking systems | 15-22% reduction in time per site |
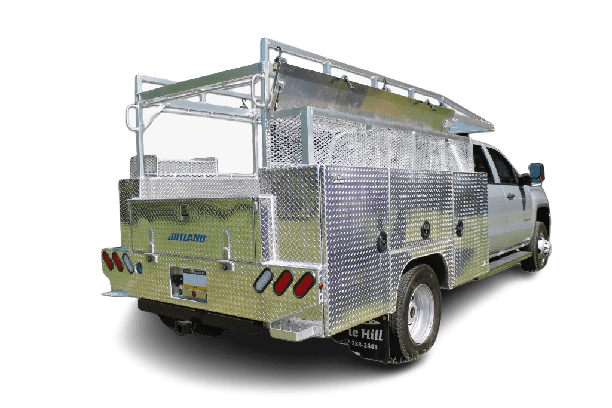
Compatibility considerations are crucial when selecting truck accessories. This is a common mistake: Purchasing accessories without confirming compatibility with specific vehicle models. Each truck model has unique dimensions, weight limitations, and mounting points. Working with suppliers to ensure perfect fit can avoid costly mistakes and potential safety issues.
Quality certifications and industry standard compliance cannot be overlooked for truck accessories. Look for accessories that meet or exceed relevant standards such as FMVSS (Federal Motor Vehicle Safety Standards) or NTEA (National Truck Equipment Association) certifications. These certifications ensure accessories meet safety and performance benchmarks.
Supplier evaluation should consider multiple factors when purchasing truck accessories. Product quality is obviously critical, but equally important are after-sales support, warranty terms, and parts availability. A mid-sized logistics company with 30 years of history shared: “We’ve learned that supplier relationships are as important as the products themselves. When issues arise, quick response and resolution capability can mean the difference between a vehicle returning to service immediately or being down for days.”
The value of long-term partnerships should not be underestimated when sourcing truck accessories. Establishing relationships with reliable suppliers can lead to customized solutions, priority support, and potential discounts. Many top suppliers also offer fleet management insights and industry best practices, adding value to the partnership.
6. What Installation Considerations Matter For Truck Accessories?
Installation decisions directly impact accessory performance and lifespan. Here’s the reality: Even the highest quality accessories can lead to problems, safety hazards, and premature failure if improperly installed.
Professional installation versus self-installation has pros and cons for truck accessories. Professional installation ensures correct mounting procedures, appropriate tools, and experienced technicians. Self-installation may save initial costs but can lead to warranty issues and potential safety risks. For critical safety components like bumpers and structural body modifications, professional installation is almost always the wiser choice.
Installation Method | Advantages | Disadvantages | Most Suitable Accessory Types |
---|---|---|---|
Professional Installation | Warranty protection, expertise, proper tools | Higher cost, requires appointment, vehicle downtime | Structural accessories, electrical systems, complex modifications |
Dealer Installation | Integration with vehicle warranty, OEM standards | Typically highest cost, limited customization options | Accessories integrating with vehicle systems |
Self-Installation | Lowest cost, flexible scheduling, learning experience | Potential errors, possible warranty issues, tool limitations | Simple non-structural accessories, interior organizational systems |
Hybrid Approach | Cost optimization, prioritization of critical components | Requires coordination, potential compatibility issues | Multi-component upgrade projects |
Installation timeline and fleet downtime impact are key considerations for truck accessories. This is critical: Each vehicle out of service represents lost productivity and potential revenue reduction. Developing a phased installation plan, scheduling vehicles during non-peak periods, and considering temporary replacement vehicles can minimize business disruption.
Common installation challenges include compatibility issues, electrical system integration, and structural modification requirements for truck accessories. Experienced installers anticipate these challenges and develop solutions. For example, installing heavy-duty bumpers may require reinforcement of frame mounting points, while complex tool box systems might need custom brackets.
A plumbing company encountered challenges when installing new accessories for their 15 service vehicles. Their fleet manager explained: “We initially planned to self-install to save costs but quickly realized the value of professional installation. The installation team identified several electrical and structural issues we hadn’t anticipated and were able to address these without damaging the vehicles or accessories.”
Post-installation inspection and quality assurance processes are essential for ensuring long-term performance of truck accessories. Comprehensive inspection should include all mounting points, electrical connections, and functional testing. Many professional installers provide detailed inspection checklists and follow-up service to address any issues that might arise.
7. How To Maximize ROI From Truck Accessory Investments?
Maximizing return on accessory investments requires strategic thinking. This is fundamental: Accessories aren’t merely costs but investments capable of providing measurable returns. Understanding how to optimize these returns is essential for wise fleet management.
Developing accessory lifecycle and maintenance plans is a critical first step. Quality truck accessories can provide years of service but require proper maintenance. Creating a schedule for regular inspection and maintenance can significantly extend lifespan and maintain performance.
Accessory Type | Expected Lifespan | Recommended Maintenance Interval | Common Failure Points |
---|---|---|---|
Aluminum Tool Boxes | 8-12 years | Inspect locks and hinges every 6 months | Lock mechanisms, seals, hinges |
Steel Tool Boxes | 5-8 years | Check for rust and seals every 3 months | Weld points, bottom edges, locks |
Heavy-Duty Bumpers | 7-10 years | Inspect mounting points and coating quarterly | Mounting bolts, coating damage, light connections |
Aluminum Bodies | 10-15 years | Annual structural and seal inspection | Door hinges, seals, electrical systems |
Bed Liners and Cargo Systems | 5-7 years | Check for wear and anchor points every 6 months | High-contact areas, anchor points, edge seals |
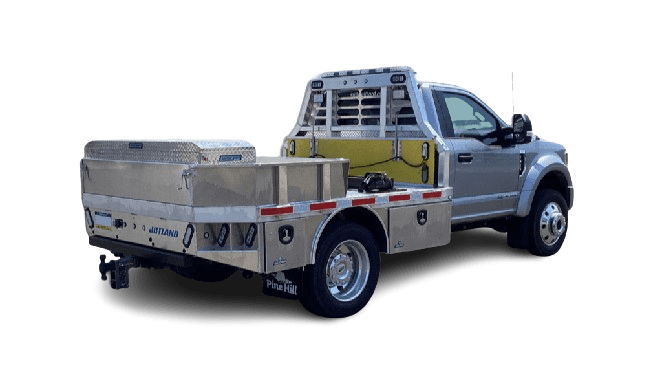
A direct relationship exists between accessory upgrades and vehicle residual value. This is interesting: Properly chosen quality accessories can actually increase vehicle resale value. A study of 500 commercial trucks found that vehicles equipped with premium aluminum tool boxes and bodies had average residual values 15-20% higher.
Understanding tax benefits and policies related to commercial vehicle modifications can further enhance ROI for truck accessories. Many jurisdictions offer tax breaks or accelerated depreciation for commercial vehicle improvements. Consulting with tax professionals about opportunities specific to your business may uncover significant savings.
Success cases demonstrate the value of strategic truck accessory investments. A medium-sized electrical contractor invested in custom aluminum tool boxes and organizational systems for their 25 service vehicles. According to Fleet Concepts’ market update, improved supply chain efficiency is creating a more stable market for both service providers and customers. The results were impressive: technicians reported saving an average of 35 minutes daily in tool search time, tool damage and replacement decreased by 42%, and customer satisfaction improved by 23%. Overall ROI analysis showed an 18-month payback period, after which each vehicle saved approximately $3,800 annually.
Efficiency Metric | Pre-Accessories | Post-Accessories | Percentage Improvement | Annual Savings (Per Vehicle) |
---|---|---|---|---|
Tool Search Time | 45 minutes daily | 10 minutes daily | 78% | $4,550 |
Fuel Efficiency | Baseline | 12% improvement | 12% | $1,800 |
Maintenance Costs | Baseline | 22% reduction | 22% | $1,250 |
Vehicle Downtime | 8 days annually | 3 days annually | 63% | $3,000 |
Tool Replacement | Baseline | 42% reduction | 42% | $950 |
With careful planning, strategic selection, and proper maintenance, truck accessory investments can provide significant returns. The key is viewing accessories as strategic business tools capable of improving efficiency, reducing costs, and ultimately enhancing profitability.
Conclusion
Proper truck accessories are vital for improving fleet efficiency. We’ve explored how tool boxes, bumpers, and aluminum bodies translate into tangible business advantages through improved organization, protection, and weight reduction. Data shows strategic accessory investments can reduce operational costs by up to 30% while extending vehicle lifespan. [Brand] offers comprehensive truck accessory solutions tailored to your specific industry needs. Contact our fleet specialists for a free consultation to learn how you can enhance your fleet performance through proper accessory selection and professional installation.
FAQ Section
Q1: What is the average lifespan of truck accessories?
Truck accessories vary in lifespan depending on materials and usage conditions. High-quality aluminum tool boxes typically last 8-12 years, while premium steel bumpers can endure 5-8 years under normal usage conditions. Aluminum bodies last even longer, with many products offering 10-15 year warranties. Regular maintenance and proper usage can significantly extend the lifespan of all accessories.
Q2: Will custom truck accessories affect my vehicle warranty?
This depends on the type of accessory and installation method. Professionally installed quality accessories typically don’t affect factory warranties, though certain modifications might impact specific component warranties. It’s advisable to consult with vehicle manufacturers or authorized dealers before installation and choose accessories that meet OEM standards. Many reputable accessory manufacturers offer their own warranties that can bridge potential factory warranty gaps.
Q3: How much more expensive are aluminum bodies compared to steel bodies?
Aluminum bodies typically cost 15-25% more initially than comparable steel specifications. However, in the long term, aluminum accessories offer better total cost of ownership through weight reduction (improving fuel efficiency), maintenance-free operation (no rust prevention needed), and higher residual value. For commercial fleets with long-term usage, the additional investment in aluminum bodies typically pays for itself within 3-5 years.
Q4: How can I ensure truck accessories meet industry safety standards?
Choose accessories that comply with FMVSS (Federal Motor Vehicle Safety Standards) and look for industry certifications such as NTEA (National Truck Equipment Association) approval. Reliable manufacturers will provide detailed safety testing data and compliance documentation. Additionally, regularly inspect accessories for wear and maintain them according to manufacturer recommendations to ensure continued safety performance.
Q5: Can custom truck accessories improve vehicle resale value?
Quality custom accessories typically enhance commercial truck resale value, particularly those that improve functionality and durability. Aluminum tool boxes and bodies especially improve resale value due to their longevity and corrosion resistance. However, overly personalized or low-quality modifications may decrease value. Best practice is to choose universal design accessories from reputable brands that are both practical and have broad market appeal.