In heavy-duty trucking, efficient tool storage is crucial. Operators face issues like disorganized tools, equipment damage, and theft, leading to downtime and financial losses. How can you enhance operational efficiency and protect your assets? A Heavy-Duty Custom Toolbox for Semi Trucks & Trailers offers a robust, tailored solution for secure, organized, and accessible storage. This article guides you through selecting the ideal custom toolbox, covering materials, installation, and maintenance, empowering you to make an informed decision for your fleet.
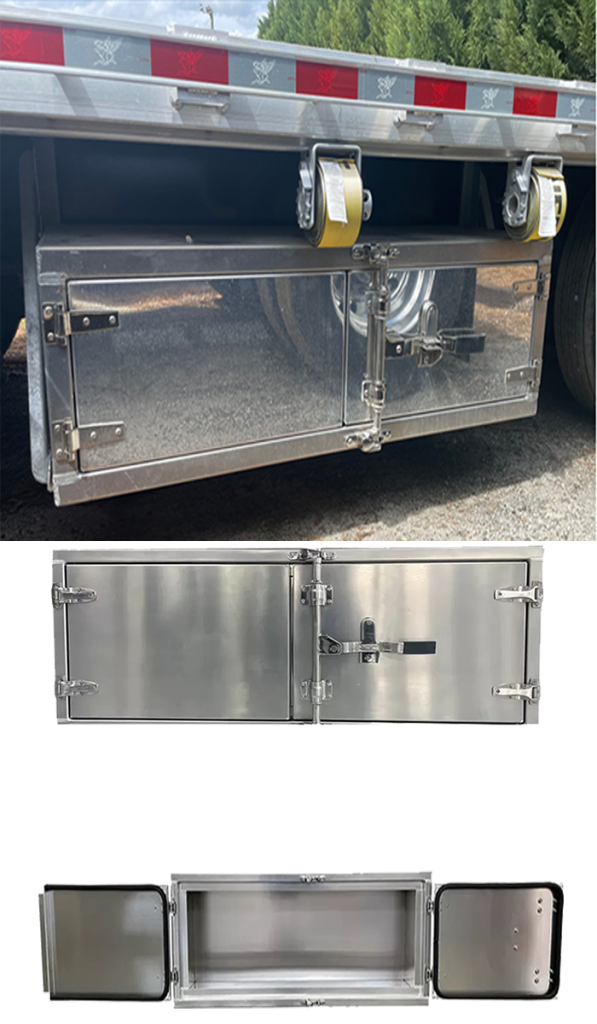
1. Why is a Custom Toolbox So Important?
A Heavy-Duty Custom Toolbox for Semi Trucks & Trailers is a strategic asset, impacting operational efficiency, safety, and equipment longevity. What makes this investment crucial?
Firstly, these toolboxes provide superior protection. Road conditions, vibrations, impacts, and extreme weather can degrade standard storage. A custom-built toolbox withstands these, safeguarding delicate instruments, power tools, and spare parts. This robust protection minimizes frequent replacements, leading to significant cost savings. For example, one fleet reduced tool replacement costs by 25% after adopting custom, weather-sealed toolboxes, directly saving on environmental and road hazard damage.
Secondly, a well-designed Heavy-Duty Custom Toolbox for Semi Trucks & Trailers boosts work efficiency. Organized, accessible tools mean less time searching and more time on productive tasks. Custom compartments, drawers, and shelving ensure every item has its place, reducing clutter and streamlining maintenance. This organization leads to faster roadside repairs, quicker inspections, and overall more efficient operations, reducing downtime and increasing profitability. A study found organized tool storage could cut repair times by up to 15%.
Thirdly, toolboxes enhance vehicle safety by securing heavy or sharp objects. Unsecured tools can become dangerous projectiles during sudden stops. Custom toolboxes feature secure locking mechanisms and robust mounting systems, keeping contents firmly in place, even in extreme conditions. This prevents tools from shifting, falling out, or causing injury, contributing to a safer environment and reducing liabilities. This is vital for B2B buyers prioritizing employee well-being and safety compliance.
Finally, a Heavy-Duty Custom Toolbox for Semi Trucks & Trailers elevates your professional image. A clean, organized, and well-equipped vehicle reflects positively on your business, conveying professionalism and reliability. This differentiates you in a competitive market, influencing client perceptions and fostering trust. Custom toolboxes can also integrate seamlessly with vehicle aesthetics, sometimes featuring company branding, turning the truck into a mobile advertisement for quality service. One trucking company saw increased client inquiries after updating their fleet with uniformly designed toolboxes, showing the impact of professional appearance.
| Benefit Category | Specific Advantage | Impact on B2B Buyers |
|—|—|—|—|
| Protection | Safeguards tools from damage, weather, theft | Reduces replacement costs, extends tool lifespan, minimizes financial loss |
| Efficiency | Organizes tools, reduces search time, streamlines operations | Decreases downtime, improves productivity, optimizes labor costs |
| Safety | Secures contents, prevents shifting and injury | Enhances driver safety, reduces liability, ensures regulatory compliance |
| Image | Projects professionalism, enhances vehicle aesthetics | Boosts brand reputation, attracts clients, differentiates in market |
These benefits show why a custom toolbox is a fundamental component for heavy-duty trucking, paying dividends in protection, efficiency, safety, and brand perception.
2. What Common Materials Are Used in Custom Toolboxes?
Material choice for a Heavy-Duty Custom Toolbox for Semi Trucks & Trailers is crucial, affecting durability, weight, cost, and environmental resistance. What are the primary materials, and how do their properties align with operational needs? Understanding these helps select an optimal toolbox.
Aluminum Alloy Toolboxes: Aluminum is popular for its strength-to-weight ratio. Its lightness reduces vehicle weight, improving fuel efficiency and payload capacity—key for B2B buyers. Aluminum also offers excellent corrosion resistance, ideal for harsh weather, road salts, and chemicals. Though pricier than steel, its longevity and low maintenance often result in a lower total cost of ownership. Modern aluminum alloys (e.g., 5052, 6061) are engineered for high strength and weldability.
Stainless Steel Toolboxes: Known for superior strength and aesthetics, stainless steel toolboxes offer maximum durability and resistance to rust and corrosion in demanding environments. Stainless steel provides robust protection against impacts and punctures, ideal for heavy or sharp tools. Its non-porous surface is easy to clean and maintain. While heavier and costlier than aluminum, its long lifespan and ruggedness make it a worthwhile investment for fleets prioritizing extreme durability and security.
Carbon Steel Toolboxes: Carbon steel offers a cost-effective solution for Heavy-Duty Custom Toolbox for Semi Trucks & Trailers, providing good strength and impact resistance. This versatile material is easily fabricated. However, it rusts without proper treatment. Carbon steel toolboxes typically undergo extensive surface treatments like powder coating, e-coating, or hot-dip galvanizing to enhance resistance and prolong lifespan. These treatments protect the steel and allow color customization, matching brand aesthetics.
Surface Treatment Processes: Regardless of the base material, surface treatment for a Heavy-Duty Custom Toolbox for Semi Trucks & Trailers is crucial for longevity and appearance. Common treatments include:
- Powder Coating: Durable, chip-resistant, corrosion-preventing. Wide color range, eco-friendly. Effective for carbon steel, creating a moisture barrier.
- Electrophoretic Coating (E-coating): Uniform, thin, highly adhesive protective layer, even for complex shapes. Excellent corrosion resistance, often used as a primer.
- Chrome Plating: Aesthetic, shiny, mirror-like finish, adds corrosion resistance. Enhances premium look on stainless steel.
- Polishing: For stainless steel and aluminum, creates a smooth, bright, easy-to-clean surface. Enhances natural beauty and provides minor corrosion resistance.
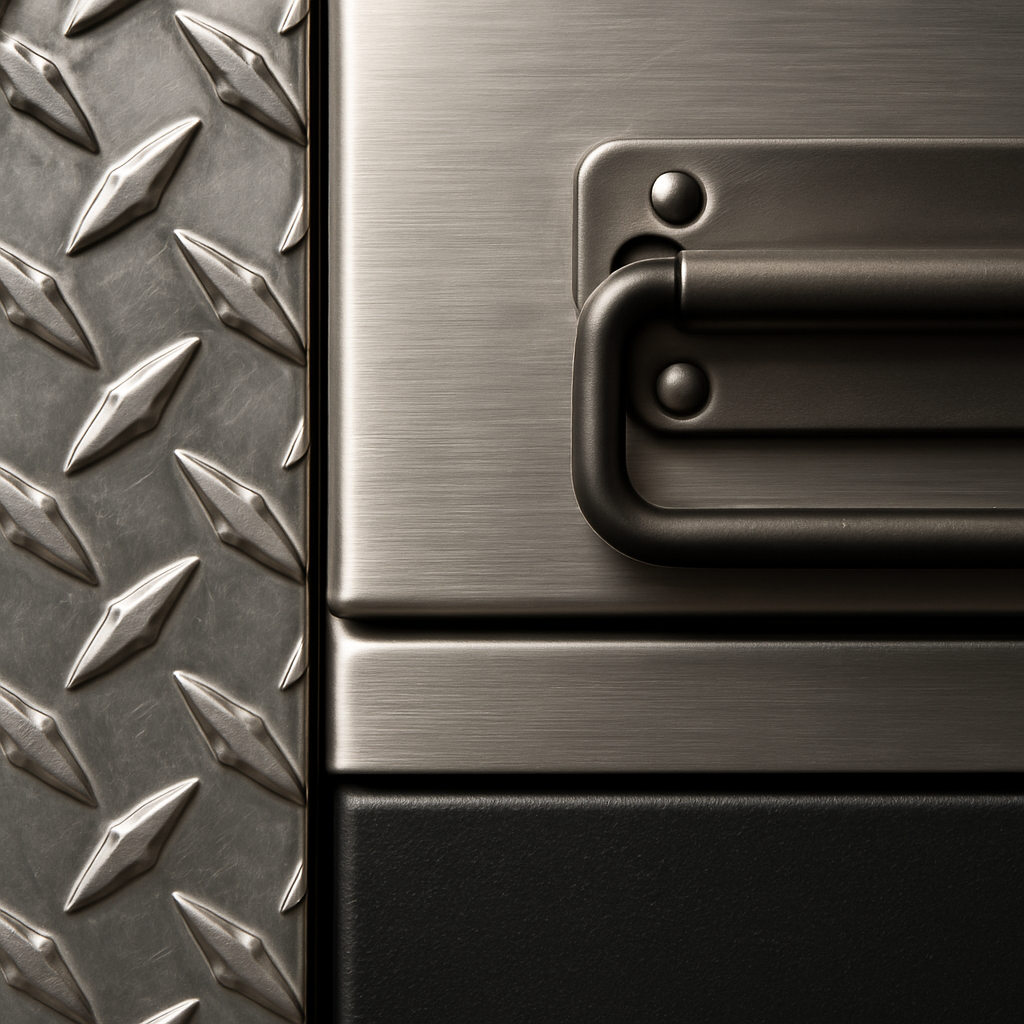
Material Type | Key Advantages | Key Considerations | Ideal Applications |
---|---|---|---|
Aluminum Alloy | Lightweight, excellent corrosion resistance, fuel efficiency potential | Higher initial cost than carbon steel, slightly less impact resistance than steel | Fleets prioritizing fuel economy, payload capacity, and corrosion resistance in humid/salty climates |
Stainless Steel | Superior strength, maximum corrosion resistance, premium appearance | Heaviest, highest cost | Extreme durability needs, high-impact environments, premium aesthetic requirements |
Carbon Steel | Cost-effective, good strength, versatile fabrication | Requires robust surface treatment for corrosion protection | Budget-conscious fleets, less corrosive environments, where weight is not a primary concern |
Selecting the right material balances operational demands, environmental exposure, budget, and aesthetics. Consulting a reputable manufacturer ensures your Heavy-Duty Custom Toolbox for Semi Trucks & Trailers meets all requirements.
3. How to Choose the Right Toolbox Design?
Choosing the right design for a Heavy-Duty Custom Toolbox for Semi Trucks & Trailers is as crucial as material selection. Design dictates accessibility, organization, and integration with your vehicle and workflow. What design options are available, and which suits your fleet best?
Side-Mount Toolboxes: Common, mounted along the truck frame. They offer convenient ground access, ideal for frequently used tools. Various lengths and depths allow flexible storage. Placement helps maintain a low center of gravity. However, size can be limited by frame space, and accessing contents might require stepping up. For fleets needing quick tool access, a side-mount Heavy-Duty Custom Toolbox for Semi Trucks & Trailers is excellent. Many models feature robust latches and weather seals. Some incorporate internal shelving or drawers for enhanced organization.
Top-Mount Toolboxes: Positioned on top of frame rails or flatbed, offering large storage and easy access from above. Useful for larger items like jacks or chains, often favored by flatbed operators. While providing ample storage, access might require climbing onto the truck bed. Top-mount Heavy-Duty Custom Toolbox for Semi Trucks & Trailers often feature robust lids with gas struts, and their elevated position offers additional security. Some designs are low-profile to minimize aerodynamic impact.
Drawer-Style Toolboxes: Feature multiple pull-out drawers for exceptional organization and easy access without rummaging. Each drawer can be customized with dividers or foam inserts to hold specific tools, preventing shifting and reducing wear. Often integrated into side-mount or under-body configurations, offering efficient and ergonomic solutions. Beneficial for technicians with many small parts and instruments, allowing quick retrieval. While potentially higher in cost, time saved and tool protection often justify the investment. Many feature heavy-duty slides and positive latching mechanisms.
Customized Designs: Beyond standard, manufacturers offer highly customized solutions for a Heavy-Duty Custom Toolbox for Semi Trucks & Trailers. This allows tailoring the toolbox to unique operational requirements, vehicle specifications, and aesthetics. Customization includes dimensions, internal layouts (e.g., diagnostic equipment compartments, charging stations), material combinations, security features (e.g., advanced locking, GPS tracking), and exterior finishes matching branding. This ensures optimal functionality and seamless integration, maximizing efficiency and reinforcing a professional image. Skilled fabricators provide innovative solutions.
When choosing a toolbox design, consider:
- Accessibility Needs: How often and from where will tools be accessed?
- Storage Capacity: What volume and type of tools need storage?
- Vehicle Integration: How will it fit with existing truck structure and accessories?
- Security Requirements: What level of security is needed?
- Budget: Balance features and materials with financial constraints.
Toolbox Design | Key Features | Advantages | Considerations |
---|---|---|---|
Side-Mount | Mounted along truck frame, accessible from ground | Easy access, maintains low center of gravity | Limited by frame space, may require stepping up for access |
Top-Mount | Mounted on frame rails or flatbed, accessible from above | Large storage capacity, ideal for bulky items | May require climbing for access, potential impact on aerodynamics |
Drawer-Style | Multiple pull-out drawers, customizable compartments | Exceptional organization, easy access to individual tools | Higher cost, complex internal mechanisms |
Customized | Tailored dimensions, internal layouts, security features, aesthetics | Optimal functionality, seamless integration, brand reinforcement | Requires detailed planning, potentially higher cost |
Choosing the right design for your Heavy-Duty Custom Toolbox for Semi Trucks & Trailers is a strategic decision impacting fleet efficiency and security. Evaluate needs and design characteristics to select a solution that protects assets and enhances operational capabilities.
4. What is the Installation Process for a Custom Toolbox?
Proper installation of a Heavy-Duty Custom Toolbox for Semi Trucks & Trailers is vital for security, stability, and longevity, preventing rattling, detachment, or vehicle damage. What steps are involved in a professional installation? Understanding this ensures your investment performs as expected.
Preparation and Planning: Thorough preparation is essential. Review manufacturer instructions, gather tools, and identify the optimal mounting location. Consider weight distribution, accessibility, and clearance from other vehicle components. Clean the mounting surface for a secure fit and to prevent corrosion.
Mounting and Securing: The core involves securely attaching the toolbox to the vehicle. This typically means drilling holes into the frame or using existing mounting points with heavy-duty bolts. The method depends on toolbox design and vehicle structure. Use appropriate torque settings for all fasteners. Many custom toolboxes include anti-vibration pads or rubber isolators for enhanced stability and noise reduction.
Electrical Connections (if applicable): Some Heavy-Duty Custom Toolbox for Semi Trucks & Trailers models have integrated lighting or power outlets. If so, proper electrical wiring is necessary. Connect the toolbox’s electrical system to the vehicle’s power source, often via a dedicated fuse. All wiring must be properly routed, secured, and protected from abrasion, heat, and moisture. Test all electrical functions after connection for safety.
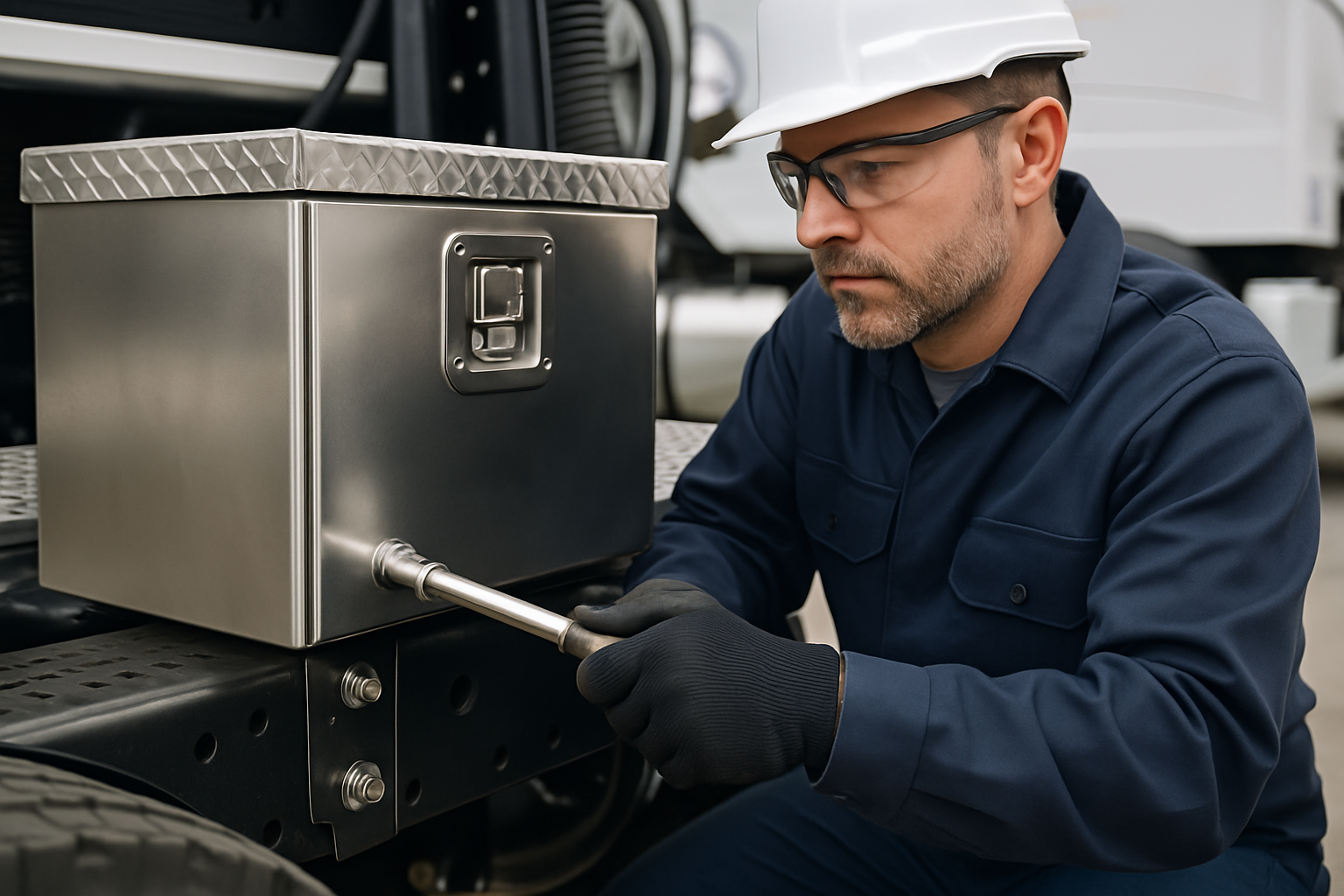
Final Inspection and Testing: After mounting and electrical connections, a comprehensive final inspection is paramount. Check all mounting points for tightness, ensure toolbox doors/drawers operate smoothly, and verify no obstruction to vehicle lights, mirrors, or sensors. A road test, if feasible, can identify rattling or instability. This final check ensures the Heavy-Duty Custom Toolbox for Semi Trucks & Trailers is securely installed, fully functional, and safe. Many manufacturers recommend a follow-up inspection after the first few hundred miles to re-torque fasteners.
| Installation Step | Key Actions | Importance for B2B Buyers |
|—|—|—|—|
| Preparation | Review instructions, gather tools, identify mounting location, clean surface | Prevents errors, ensures proper fit, saves time and resources |
| Mounting | Securely attach with appropriate hardware and torque settings | Guarantees stability, prevents detachment, protects vehicle and contents |
| Electrical (if applicable) | Route and secure wiring, connect to power, test functions | Ensures safe operation of features, prevents electrical faults |
| Final Inspection | Check tightness, functionality, and clearances; road test | Confirms safety, optimizes performance, avoids future issues |
Adhering to these guidelines ensures your Heavy-Duty Custom Toolbox for Semi Trucks & Trailers provides reliable service and maximum protection. Professional installation is often recommended for complex setups or warranty compliance.
5. What Are the Maintenance and Care Tips for Toolboxes?
Investing in a Heavy-Duty Custom Toolbox for Semi Trucks & Trailers is a long-term commitment. Regular maintenance and care are essential to ensure it continues to pay dividends. How can you maximize its lifespan and functionality? A consistent routine preserves its integrity, appearance, and content security.
Regular Cleaning and Corrosion Prevention: Road environments expose toolboxes to dirt, grime, and chemicals. Regular cleaning prevents buildup leading to corrosion. Use mild soap and water; avoid abrasives. For stainless steel or aluminum, a simple wash suffices. For carbon steel, pay attention to chipped areas, as they are vulnerable to rust. Promptly touching up damaged areas with rust-inhibiting paint extends its life. Fleets in coastal areas or with heavy road salting may need more frequent cleaning and specialized inhibitors.
Maintenance of Locks and Hinges: Security and accessibility rely on proper lock and hinge function. Inspect them regularly for wear, rust, or damage. Lubricate with weather-resistant lubricant for smooth operation. Address stiffness or grinding immediately to prevent security breaches or failure. Advanced toolboxes with stainless steel hinges and automotive-grade locks require less frequent but equally important maintenance.
Internal Organization and Moisture Prevention: While the exterior protects, the interior needs attention to protect tools. Moisture can accumulate, causing rust. Ensure adequate drainage or ventilation. Use desiccant packets or moisture-absorbing liners in humid climates. Regularly organize contents to prevent shifting and damage. Foam inserts, rubber mats, or custom dividers keep tools organized and provide cushioning. A well-organized interior also helps spot missing tools.
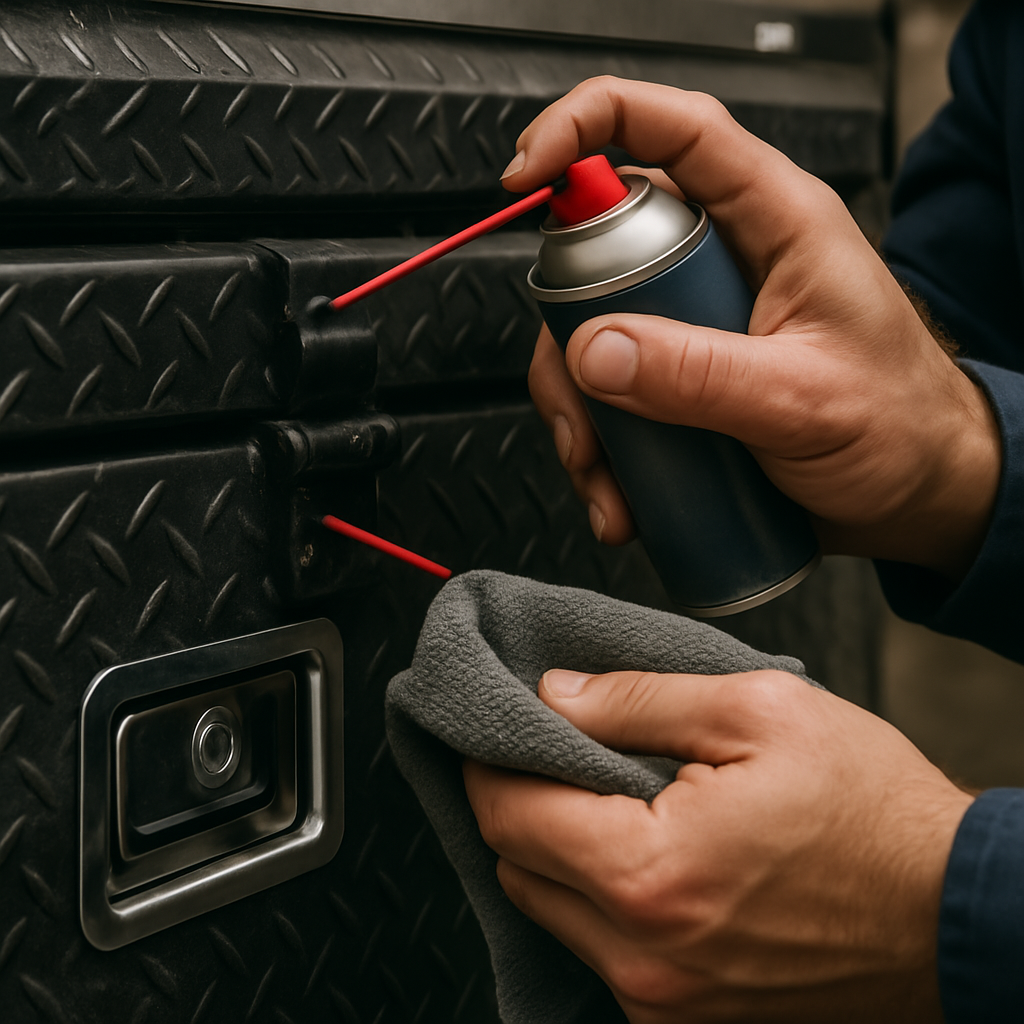
Regular Inspection and Repair: Beyond routine care, a comprehensive inspection schedule is vital. Periodically check mounting hardware for tightness, as vibrations can loosen bolts. Inspect the toolbox body for cracks, dents, or structural damage. Address minor repairs promptly, like replacing worn weather stripping. Ignoring small issues leads to bigger problems. For complex repairs, consult a professional to ensure proper repair and maintained protective capabilities. This proactive approach ensures your toolbox remains a reliable asset.
| Maintenance Area | Key Actions | Benefit for B2B Buyers |
|—|—|—|—|
| Cleaning | Regular washing, touch-up damaged coatings | Prevents corrosion, maintains appearance, extends lifespan |
| Locks/Hinges | Lubricate, inspect for wear/damage | Ensures security, maintains accessibility, prevents costly repairs |
| Internal | Moisture control, organization, cushioning | Protects tools from rust/damage, improves efficiency, reduces tool replacement |
| Inspection/Repair | Check mounting, structural integrity, address minor issues | Prevents major failures, ensures safety, maximizes ROI |
Implementing these tips ensures your Heavy-Duty Custom Toolbox for Semi Trucks & Trailers provides secure, organized, and reliable storage, contributing to fleet efficiency and profitability.
6. How Does a Custom Toolbox Affect Vehicle Performance?
A Heavy-Duty Custom Toolbox for Semi Trucks & Trailers primarily provides storage, but its integration can influence vehicle performance. Understanding these impacts helps fleet managers make informed choices balancing functionality and efficiency. Are you aware of all the ways a toolbox can impact your truck?
Impact on Vehicle Load Capacity: Adding a custom toolbox, especially a heavy one filled with tools, increases overall vehicle weight. This reduces available payload capacity. For fleets operating near maximum GVWR, this is significant. Calculate the toolbox and contents weight to ensure it doesn’t exceed legal limits or compromise structural integrity. Lightweight materials like aluminum can mitigate this.
Impact on Fuel Efficiency: Added weight and aerodynamic changes can affect fuel efficiency. While weight is more significant, a large, poorly designed toolbox can create drag. Even a small percentage decrease in fuel efficiency across a fleet translates to substantial operational cost increases. Manufacturers design custom toolboxes with aerodynamic considerations to minimize this effect. Selecting a lightweight toolbox and mounting it to not disrupt airflow helps preserve fuel economy.
Impact on Vehicle Balance: Toolbox placement influences vehicle balance and center of gravity. If a heavy toolbox is mounted disproportionately or too high, it affects handling, especially during turns or on uneven terrain. Proper weight distribution is critical for stability and safety. Professional installation services consider existing weight distribution and recommend optimal mounting locations. This might involve multiple smaller toolboxes or strategic content distribution for even loading.
Impact on Vehicle Appearance: While not a direct performance metric, the aesthetic integration of a Heavy-Duty Custom Toolbox for Semi Trucks & Trailers significantly contributes to the fleet’s professional image. A well-designed and properly installed toolbox enhances the truck’s appearance, reflecting positively on the business. Customization options, such as matching paint colors, polished finishes, or integrated branding, ensure the toolbox complements the vehicle’s design and reinforces company brand identity. This visual consistency can be an effective marketing tool.
| Performance Aspect | Potential Impact | Mitigation Strategies |
|—|—|—|—|
| Load Capacity | Reduced available payload | Choose lightweight materials (e.g., aluminum), calculate weight carefully, distribute contents evenly |
| Fuel Efficiency | Slight decrease due to added weight/drag | Select aerodynamic designs, opt for lighter materials, ensure proper mounting |
| Vehicle Balance | Affected handling, stability issues | Professional installation, strategic placement, even weight distribution |
| Appearance | Enhanced or detracted professional image | Choose complementary designs, customize finishes, integrate branding |
By carefully considering these performance aspects during the selection and installation of a Heavy-Duty Custom Toolbox for Semi Trucks & Trailers, businesses can ensure they gain the benefits of secure storage without compromising operational efficiency, safety, or professional image. It’s about making an informed decision that supports both practical needs and long-term business goals.
Conclusion
This guide provides a deeper understanding of selecting, installing, and maintaining the ideal Heavy-Duty Custom Toolbox for Semi Trucks & Trailers. This investment is strategic, impacting operational efficiency, equipment safety, driver safety, and brand image. Prioritizing robust materials, ergonomic designs, and meticulous installation and maintenance extends tool lifespan, minimizes downtime, and ensures peak fleet performance. Ready to optimize your fleet’s efficiency and security? Partner with Morton today to find the perfect custom toolbox solution tailored to your needs, and take the next step towards a more organized, productive, and secure trucking operation. Visit our website or contact our experts to discuss how our custom solutions can benefit your business.
FAQ Section
Q1: What is the average cost of a custom toolbox?
The cost varies widely based on material, size, design, and customization. Aluminum toolboxes range from $500-$2,000; stainless steel or highly customized units can exceed $3,000. Installation costs are separate. Consider long-term value from enhanced protection and efficiency.
Q2: Can a toolbox affect the vehicle’s warranty?
Generally, installing an aftermarket toolbox should not void a vehicle’s warranty if done correctly and without modifying warranted components. However, improper installation leading to damage might not be covered. Consult your vehicle manufacturer’s warranty and consider professional installation.
Q3: How to ensure the anti-theft performance of the toolbox?
Maximize anti-theft by choosing robust materials (thick-gauge steel/aluminum) with high-security locking mechanisms (puck locks, multi-point latching). Ensure secure mounting to prevent easy removal. Consider alarms or GPS trackers for high-value contents. Proper, out-of-sight placement also deters thieves.
Q4: How long does a custom toolbox typically last?
Lifespan depends on material, construction, and maintenance. A well-maintained, high-quality aluminum or stainless steel toolbox can last 10-20 years or more. Carbon steel with proper anti-corrosion treatment also offers longevity. Regular cleaning, lubrication, and prompt repair extend service life.
Q5: Where can I find reliable custom toolbox suppliers?
Find reliable suppliers through industry trade shows, online truck accessory directories, and referrals. Look for manufacturers with strong reputations for quality, customization, and customer service. Check reviews, request specifications, and inquire about warranty and after-sales support.