Are you struggling to find the right protection for your semi truck fleet? Standard bumpers often fail during minor collisions, leading to costly repairs and extended downtime. Custom bumpers designed specifically for semi trucks can provide superior protection, reduce maintenance costs, and extend vehicle lifespan. With over 20 years of experience in the heavy-duty trucking industry, we’ve seen properly designed custom bumpers reduce front-end damage by up to 70% and save fleet operators thousands in repair costs annually.
1. Why Do Semi Trucks Need Custom Bumpers?
Standard factory bumpers on semi trucks are primarily designed for basic protection and aesthetics, not for the demanding conditions these vehicles regularly face. Here’s the truth: factory bumpers simply aren’t built to withstand the rigors of commercial trucking operations. Their lightweight construction and limited reinforcement make them vulnerable to damage from even minor impacts.
The unique challenges semi trucks face on the road make custom bumpers a necessity rather than a luxury. Long-haul trucks encounter debris, wildlife collisions, and minor accidents at a much higher rate than passenger vehicles due to their extensive mileage. Highway driving at high speeds increases the potential impact force, while off-highway operations expose trucks to rough terrain and obstacles that standard bumpers aren’t designed to handle.
Road Challenge | Impact on Standard Bumpers | Custom Bumper Solution |
---|---|---|
Highway debris | Denting, bending, component damage | Reinforced steel construction with impact absorption |
Wildlife collisions | Severe damage, radiator exposure | Full-width protection with grille guards |
Loading dock impacts | Crumpling, misalignment | Heavy-gauge steel with reinforced mounting points |
Off-road conditions | Undercarriage exposure, bumper separation | Extended lower protection and frame tie-ins |
The impact of custom bumpers on driver and vehicle safety cannot be overstated. You need to know this: a properly designed custom bumper serves as the first line of defense in a collision. By absorbing and distributing impact forces, these bumpers can prevent damage to critical components like radiators, headlights, and even frame rails. This protection translates directly to driver safety by maintaining the structural integrity of the cab in the event of a collision.
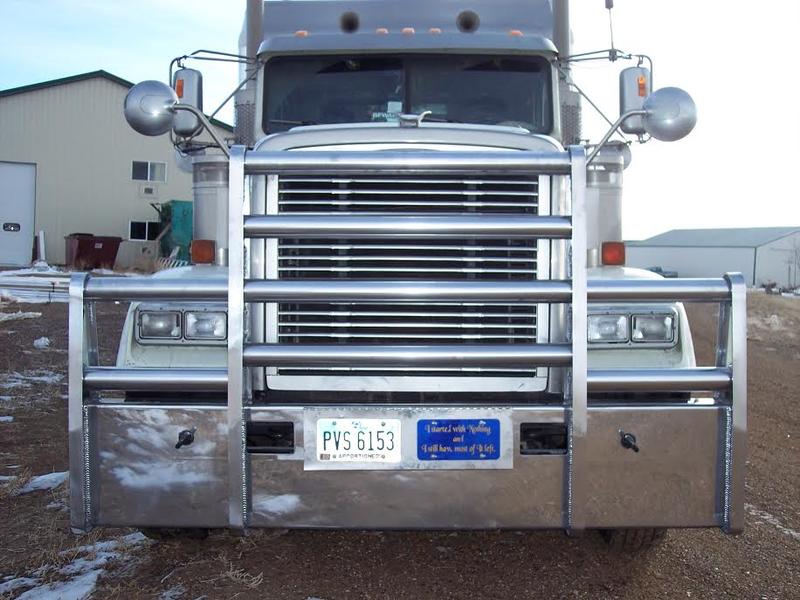
Regulatory compliance and insurance considerations also favor custom bumpers. Many insurance providers offer reduced premiums for trucks equipped with high-quality custom bumpers due to their proven ability to minimize damage in common accident scenarios. While all bumpers must meet Department of Transportation (DOT) standards, quality custom manufacturers design their products to meet or exceed these requirements while providing enhanced protection.
A logistics company with a fleet of 50 semi trucks reported that after installing custom bumpers across their fleet, they experienced a 65% reduction in front-end repair costs and a 40% decrease in downtime related to minor collisions. The initial investment was recouped within 18 months through reduced repair costs and improved operational efficiency.
2. What Materials Make The Best Bumpers?
The material selection for custom semi truck bumpers significantly impacts performance, durability, and weight. Let me be clear: not all bumper materials are created equal, and choosing the right one depends on your specific operational needs.
Steel grades vary widely in strength and weight characteristics. Commercial-grade steel (A36) offers good durability at a lower price point but adds considerable weight. High-strength low-alloy steel (HSLA) provides better strength-to-weight ratios and is commonly used in mid-range bumpers. For premium applications, chrome-moly steel (4130) delivers exceptional strength and impact resistance while keeping weight manageable.
Steel Type | Strength Rating (PSI) | Weight Impact | Corrosion Resistance | Best Application |
---|---|---|---|---|
A36 Commercial | 36,000 | Heaviest (+180-250 lbs) | Low-Moderate | Budget-conscious operations |
HSLA | 50,000-70,000 | Moderate (+150-200 lbs) | Moderate | General purpose, everyday use |
Chrome-Moly (4130) | 63,000-97,000 | Lighter (+120-180 lbs) | Moderate | Performance-focused applications |
Stainless Steel | 30,000-100,000 | Moderate-Heavy | Excellent | Corrosive environments, appearance priority |
Aluminum alloy options present compelling advantages for certain applications. This is worth noting: aluminum bumpers typically weigh 40-60% less than comparable steel versions. This weight reduction can translate to increased payload capacity and improved fuel efficiency. Modern aluminum alloys (particularly 6061-T6 and 7075) offer impressive strength characteristics, though still not matching high-grade steel. The natural corrosion resistance of aluminum eliminates the need for regular rust prevention treatments, reducing maintenance requirements.
Composite materials are emerging as specialized solutions for specific applications. Fiberglass-reinforced plastic (FRP) and carbon fiber composites offer exceptional weight savings and good impact absorption characteristics. However, their application in semi truck bumpers remains limited due to higher costs and reduced durability in extreme conditions. These materials typically find use in specialized applications where weight reduction is the absolute priority.
Material choice directly affects fuel efficiency and payload capacity. A typical steel front bumper can add 150-250 pounds to a truck’s weight, while an aluminum alternative might add only 80-120 pounds. For fleets covering extensive mileage, this weight difference can yield measurable fuel savings. A study of 25 long-haul trucks showed that those equipped with aluminum bumpers averaged 0.4% better fuel economy compared to identical trucks with steel bumpers—a small percentage that translates to significant savings across a fleet.
Material | Weight Comparison | Fuel Efficiency Impact | Durability Rating | Average Cost Range |
---|---|---|---|---|
Steel | Baseline | Baseline | Excellent | $800-$2,500 |
Aluminum | 40-60% lighter | 0.3-0.5% improvement | Good | $1,200-$3,000 |
Stainless Steel | 5-10% heavier than steel | 0.1-0.2% reduction | Excellent | $1,500-$3,500 |
Composite | 60-70% lighter | 0.5-0.7% improvement | Moderate | $2,000-$4,000 |
3. How Do Custom Bumpers Improve Performance?
Custom bumpers do far more than just protect your semi truck—they can actively enhance overall vehicle performance. The data shows: properly designed custom bumpers can improve aerodynamics, functionality, and long-term operating costs.
Aerodynamic design impacts fuel economy in significant ways. Traditional flat-faced bumpers create considerable drag, especially at highway speeds. Modern custom bumpers often incorporate curved surfaces, air dams, and flow-through designs that reduce wind resistance. Testing has shown that aerodynamically optimized bumpers can improve fuel efficiency by 1-3% compared to standard flat designs—a substantial saving for vehicles covering 100,000+ miles annually.
Integrated towing and recovery points represent a major functional improvement over standard bumpers. Quality custom designs incorporate reinforced attachment points for hooks, shackles, and winches, rated for the heavy loads associated with semi truck recovery. These integrated recovery points eliminate the need for makeshift solutions during roadside emergencies and prevent damage to frame components that weren’t designed for towing forces.
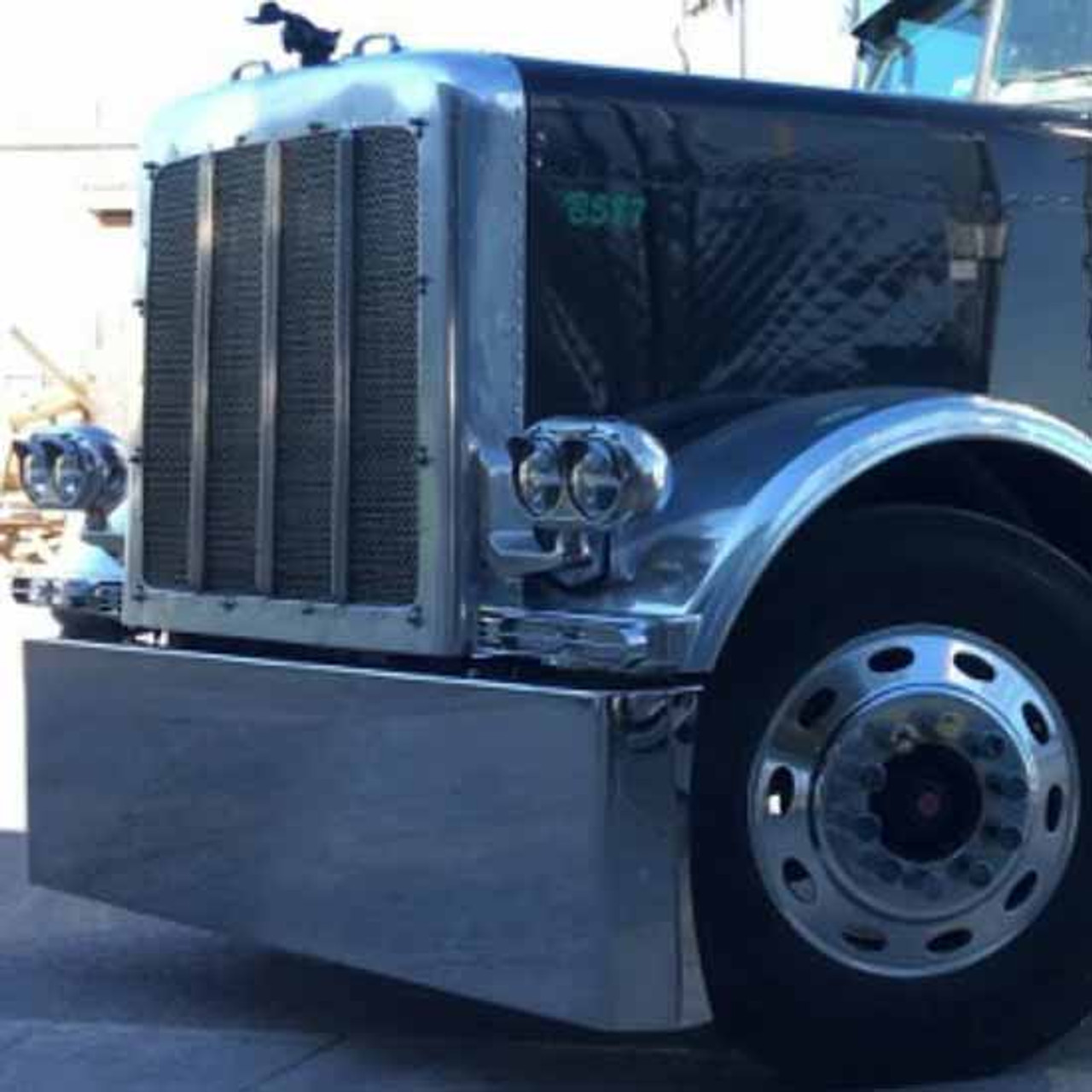
Enhanced vehicle protection translates directly to reduced maintenance costs. Consider this example: a fleet of 30 semi trucks operating in a region with high deer collision rates installed custom bumpers with integrated grille guards. Over a three-year period, they experienced 22 wildlife impacts that would typically require radiator replacement and extensive downtime. With the custom bumpers, only three incidents resulted in radiator damage, saving approximately $76,000 in repairs and preventing an estimated 45 days of vehicle downtime.
Performance data from collision tests and real-world applications consistently demonstrate the value of custom bumpers. Laboratory crash tests at 5-10 mph show that quality custom bumpers can prevent damage to critical components in impacts that would disable trucks with standard bumpers. A transportation company operating in mountainous terrain reported that trucks equipped with custom bumpers required 62% fewer front-end repairs and experienced 47% less downtime related to minor collisions compared to identical vehicles with standard equipment.
Performance Metric | Standard Bumper | Custom Bumper | Improvement Percentage |
---|---|---|---|
Low-speed impact resistance (5 mph) | Component damage likely | Minimal to no damage | 70-90% reduction in damage |
Wildlife collision protection | Radiator exposure | Protected critical components | 60-80% reduction in major damage |
Aerodynamic efficiency | Baseline | Reduced drag coefficient | 1-3% fuel economy improvement |
Recovery capability | Limited or none | Integrated rated recovery points | 100% improvement in recovery options |
Corrosion resistance (steel) | 2-3 years before visible rust | 5-7 years with proper treatment | 100-150% longer aesthetic lifespan |
4. Which Features Matter For Fleet Operations?
When managing a commercial fleet, certain bumper features deliver more operational value than others. Let’s get practical: the right features can dramatically improve safety, efficiency, and functionality across your entire operation.
Integrated LED lighting systems provide significant safety and visibility advantages. Modern custom bumpers can incorporate powerful LED work lights, auxiliary driving lights, and even warning strobes directly into the bumper structure. This integration protects the lighting from damage while providing improved illumination exactly where needed. Properly positioned LED lighting can increase forward visibility by up to 200% compared to standard headlights alone, reducing nighttime accident rates and improving driver confidence in poor conditions.
Lighting Feature | Operational Benefit | Safety Impact | Maintenance Consideration |
---|---|---|---|
Integrated LED driving lights | 150-200% increased forward visibility | Reduced nighttime accident risk | 50,000+ hour lifespan vs. 1,000 for halogens |
Work lights | Illuminated loading/unloading areas | Safer nighttime operations | Protected mounting reduces damage frequency |
Warning/strobe options | Increased vehicle visibility | Reduced struck-by incidents | Integrated wiring eliminates exposed connections |
Turn signal/marker integration | Compliant with height regulations | Better signaling visibility | Simplified electrical system |
Winch mounting options dramatically enhance self-recovery capabilities. This matters because: a truck equipped with a properly mounted winch can often extract itself from minor stuck situations without waiting for expensive recovery services. Quality custom bumpers offer reinforced winch mounts rated for 12,000-30,000 pounds, with proper frame tie-ins to distribute pulling forces safely. This capability can reduce recovery costs and minimize downtime in remote or difficult operating environments.
Modular design and component replacement simplicity can significantly reduce repair costs and downtime. The best custom bumpers utilize a sectional design that allows damaged portions to be replaced individually rather than requiring complete bumper replacement. This approach can reduce repair costs by 40-70% in common damage scenarios. For example, replacing a damaged corner section might cost $300-500 compared to $1,500-2,500 for a complete bumper assembly.
Compatibility and fleet standardization considerations are particularly important for operations managing multiple vehicles. Standardizing on a specific bumper design across compatible truck models simplifies parts inventory, streamlines maintenance procedures, and ensures consistent performance across the fleet. Many custom bumper manufacturers offer design families that maintain consistent mounting patterns and feature sets across different truck makes and models.
Fleet Standardization Aspect | Operational Benefit | Cost Impact |
---|---|---|
Consistent mounting hardware | Simplified installation process | 15-25% reduced installation labor |
Interchangeable components | Reduced parts inventory requirements | 20-30% lower parts stocking costs |
Uniform recovery points | Standardized recovery procedures | Reduced training requirements |
Common lighting configurations | Consistent electrical connections | Simplified troubleshooting |
5. What Installation Factors Should Be Considered?
The installation process for custom semi truck bumpers involves critical decisions that affect performance, warranty, and downtime. Here’s what you should know: even the highest quality bumper can fail if improperly installed.
Professional installation versus self-installation presents a clear trade-off between upfront costs and long-term reliability. Professional installation typically adds $500-1,000 to the project but includes proper alignment, secure mounting, electrical integration, and often a workmanship warranty. Self-installation may save these costs but introduces risks of improper mounting, misalignment, and potential warranty issues with both the bumper and possibly the truck manufacturer.
Installation Method | Average Cost | Pros | Cons | Best For |
---|---|---|---|---|
Professional Shop | $500-$1,000 + parts | Warranty protection, proper alignment, electrical expertise | Higher upfront cost, scheduling requirements | New bumpers with electrical components |
Dealer Installation | $800-$1,500 + parts | OEM warranty protection, factory specifications | Highest cost, limited customization options | Newer trucks under warranty |
Fleet Maintenance Team | Labor cost only | Controlled scheduling, consistent procedures | Requires proper equipment and expertise | Fleets with experienced mechanics |
Owner/Operator DIY | Materials only ($50-$150) | Lowest direct cost, flexible timing | Risk of improper installation, potential warranty issues | Simple bumpers with minimal electrical work |
Frame modification requirements vary significantly based on bumper design and truck model. Some custom bumpers are designed as direct replacements requiring no frame modifications, while others may need additional brackets, reinforcement plates, or even frame extensions. This is critical: any frame modifications must be performed correctly to maintain structural integrity and avoid creating stress points that could lead to frame rail cracking or failure.
Installation timeline and fleet downtime impact require careful planning, especially for larger operations. A typical professional installation takes 4-8 hours per truck, depending on complexity. For fleets, staggering installations during regular maintenance intervals can minimize operational disruption. Some bumper manufacturers offer installation programs where multiple trucks can be completed in sequence to reduce overall downtime.
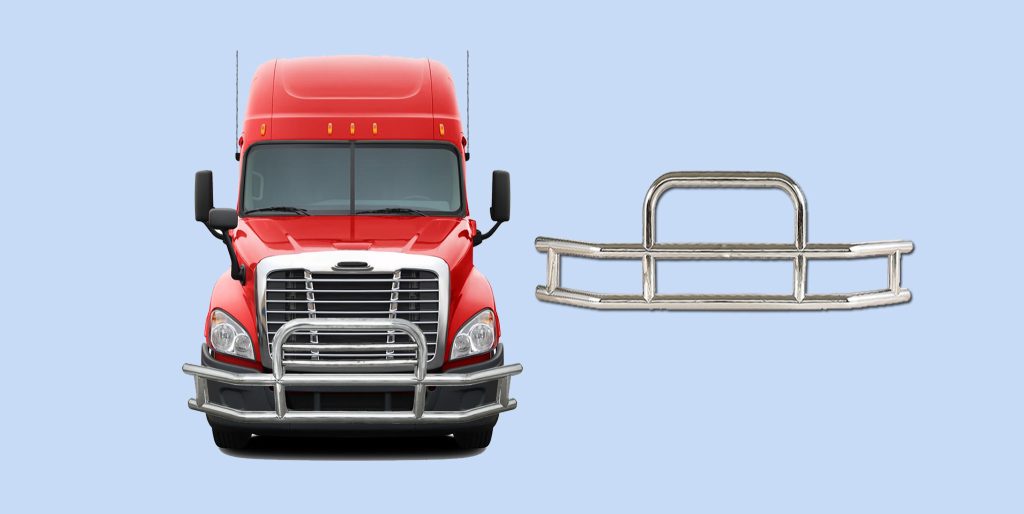
Common installation challenges include electrical integration, alignment issues, and clearance problems. Electrical integration for lighting systems often presents the most complexity, particularly when adding auxiliary functions like fog lights or work lights. Proper alignment is essential not only for appearance but also for aerodynamic performance and to prevent uneven stress distribution. Clearance issues with components like hood opening mechanisms, air intake systems, or steering components must be addressed during installation to prevent operational problems.
A regional delivery company learned this lesson the hard way when they attempted in-house installation of custom bumpers across their fleet of 12 trucks. Improper mounting led to frame stress cracks on two vehicles and misalignment issues on several others. The company ultimately spent more correcting these problems than they would have paid for professional installation, not counting the additional downtime and operational disruption.
Post-installation inspection and quality assurance processes should include:
- Verification of all mounting hardware torqued to specification
- Alignment check with the truck’s frame and body lines
- Functional testing of all integrated lighting and accessories
- Road test to check for vibration, noise, or interference issues
- Documentation of installation details for warranty purposes
6. How To Evaluate Cost Versus Value?
Making the right investment decision requires looking beyond the initial price tag to understand the true value proposition of custom bumpers. The numbers tell the story: while quality custom bumpers require significant upfront investment, their long-term financial benefits often outweigh the initial costs.
Initial investment versus long-term ownership costs present a clear picture when properly analyzed. Premium custom bumpers typically range from $1,500 to $4,000 depending on material, design complexity, and features. While this represents a substantial upfront cost compared to standard replacements ($500-$1,000), the extended lifespan and reduced repair frequency dramatically change the equation over time.
Cost Factor | Standard Bumper | Mid-Range Custom | Premium Custom |
---|---|---|---|
Initial Purchase | $500-$1,000 | $1,500-$2,500 | $2,500-$4,000 |
Installation | $200-$400 | $400-$700 | $600-$1,000 |
Average Lifespan | 3-5 years | 7-10 years | 10-15+ years |
Annual Maintenance | $100-$200 | $50-$100 | $25-$75 |
Repair Frequency | Every 1-2 years | Every 3-5 years | Every 5-8 years |
10-Year Total Cost | $3,000-$5,000 | $2,500-$4,000 | $3,500-$5,500 |
Bumper quality directly impacts maintenance cycles and costs. Standard bumpers typically require regular attention to address rust, loose mounting hardware, and minor damage. Quality custom bumpers, particularly those made from aluminum or stainless steel, dramatically reduce these maintenance requirements. A survey of fleet maintenance records showed that trucks with premium custom bumpers averaged 72% fewer bumper-related maintenance entries compared to those with standard equipment.
Return on investment calculations must consider multiple factors beyond the bumper itself. The math works like this: when calculating ROI, include reduced repair costs, decreased downtime, lower insurance premiums (where applicable), and extended vehicle service life. For example, a custom bumper that prevents just one radiator replacement ($1,200-$1,800) and the associated 2-3 days of downtime ($400-$600 per day) has already justified a significant portion of its cost premium.
A concrete example comes from a regional construction company that equipped 15 of their 30 semi trucks with premium custom bumpers as a test program. Over a three-year period, the equipped trucks required an average of $850 less in front-end repairs annually and experienced 1.3 fewer days of repair-related downtime per truck. The company calculated their true ROI at 22 months, after which the custom bumpers represented ongoing operational savings.
ROI Factor | Potential Annual Savings | Calculation Method |
---|---|---|
Repair Cost Reduction | $600-$1,200 per truck | Historical repair costs × expected reduction percentage |
Downtime Reduction | $800-$1,800 per truck | Average downtime days saved × daily operating value |
Insurance Premium Reduction | $100-$300 per truck | Annual premium × discount percentage (if offered) |
Extended Vehicle Life | $200-$500 per truck | Replacement cost ÷ extended years of service |
Fuel Savings (aerodynamic designs) | $300-$700 per truck | Annual fuel cost × efficiency improvement percentage |
7. What Maintenance Ensures Maximum Lifespan?
Proper maintenance dramatically extends the service life and performance of custom bumpers. You’ll want to remember: even the highest quality bumper requires regular attention to deliver its full value potential.
Regular inspection and preventive maintenance schedules should be integrated into routine vehicle service. For steel bumpers, quarterly inspections should check for rust formation, particularly at mounting points and welded joints. Aluminum bumpers benefit from semi-annual inspections focusing on mounting hardware tightness and structural integrity. All bumpers should have lighting and electrical connections checked monthly, especially in harsh operating conditions.
Bumper Type | Inspection Frequency | Key Inspection Points | Maintenance Actions |
---|---|---|---|
Steel | Quarterly | Rust formation, weld integrity, mounting hardware | Clean, treat rust spots, tighten hardware |
Aluminum | Semi-annually | Mounting hardware, stress cracks, electrical connections | Tighten hardware, check for galvanic corrosion |
Stainless Steel | Semi-annually | Mounting points, surface finish, electrical connections | Clean, check hardware torque |
Chrome-Plated | Quarterly | Chrome integrity, underlying rust, mounting security | Clean, treat exposed areas, protect with wax |
Surface treatment and corrosion protection methods vary by material. Steel bumpers require the most attention, benefiting from regular cleaning and application of rust-inhibiting compounds, particularly after exposure to road salt or chemical de-icers. Chrome-plated bumpers need regular polishing and protective waxing to maintain their appearance and prevent underlying corrosion. Aluminum bumpers require minimal surface treatment but benefit from occasional cleaning and inspection for galvanic corrosion where they contact dissimilar metals.
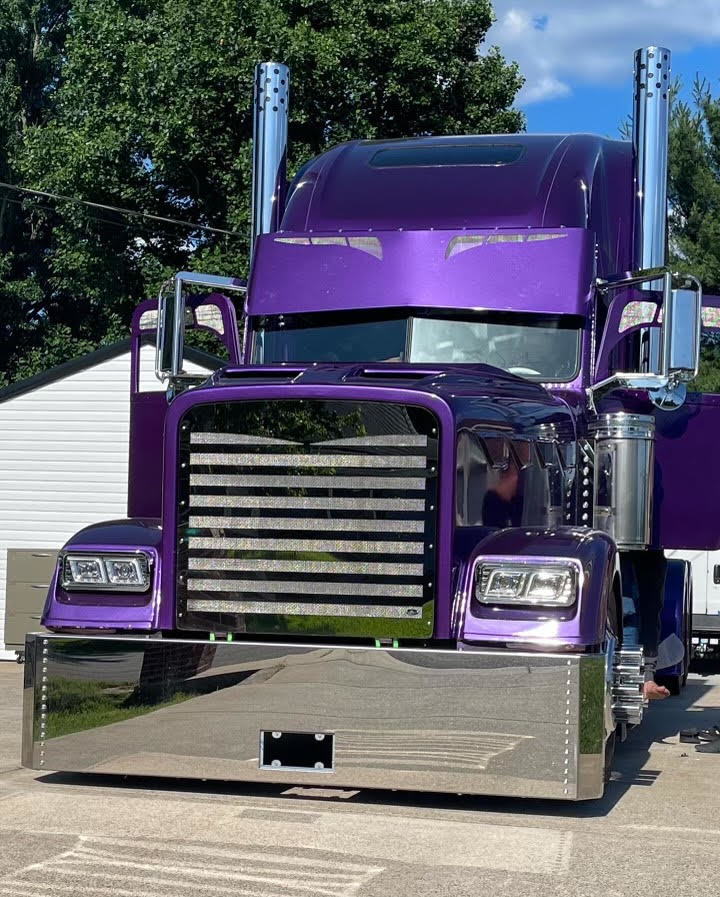
Common failure points and solutions should be understood by maintenance personnel. Mounting hardware represents the most frequent failure point across all bumper types. Using grade 8 hardware and applying proper torque specifications can prevent most of these issues. Electrical connections for integrated lighting systems benefit from dielectric grease application and proper wire routing to prevent chafing. Weld joints on steel bumpers should be inspected for crack formation, particularly after impacts or in high-vibration applications.
A preventive approach pays dividends, as demonstrated by a regional fuel delivery company. After experiencing several bumper failures due to mounting hardware issues, they implemented a monthly torque check procedure. This simple 10-minute inspection reduced bumper-related issues by 85% and eliminated several instances of bumpers becoming partially detached during operation—a potentially dangerous situation that could have resulted in road hazards or accidents.
Maintenance adjustments for extreme conditions are necessary for many operations. This is practical advice: trucks operating in severe environments require modified maintenance schedules. In winter operations with heavy road salt exposure, monthly rather than quarterly inspections of steel bumpers are warranted, along with more frequent rust treatment. Off-road operations should include post-trip inspections of mounting hardware due to increased vibration. Hot, humid environments accelerate corrosion and may require additional protective treatments for steel components.
Operating Condition | Maintenance Adjustment | Reasoning |
---|---|---|
Heavy road salt exposure | Monthly inspections, additional rust treatment | Salt accelerates corrosion process |
Off-road/rough terrain | Post-trip mounting hardware checks | Vibration can loosen fasteners rapidly |
Extreme heat/humidity | Additional protective coatings, more frequent inspection | Accelerated corrosion in these conditions |
Frequent wildlife impacts | Regular structural inspection | Cumulative damage may not be immediately visible |
High-mileage operations | Scheduled hardware replacement | Preventive replacement before failure occurs |
Conclusion
Custom bumpers represent a critical investment in semi truck protection and performance. We’ve examined how quality bumpers provide superior protection through advanced materials like chrome-moly steel and aircraft-grade aluminum, reducing repair costs by up to 70%. Data shows that fleets using custom bumpers experience 40-60% less downtime from minor collisions and save thousands in annual maintenance costs. [Brand] offers industry-leading custom bumper solutions engineered specifically for your fleet’s operational needs. Contact our team today for a personalized consultation to determine which custom bumper options will deliver the best protection and ROI for your specific semi truck applications.
FAQ Section
Q1: Are custom bumpers legal on commercial semi trucks?
Yes, custom bumpers are legal on commercial semi trucks, provided they comply with Federal Motor Vehicle Safety Standards (FMVSS) and state regulations. Key requirements include not interfering with vehicle lighting systems, having no sharp edges, not exceeding specific width limitations, and not significantly altering the vehicle’s crash characteristics. Professional manufacturers design custom bumpers to meet or exceed these standards and typically provide compliance documentation. Always verify that any custom bumper you purchase meets applicable regulations for your operating region.
Q2: How much weight do heavy-duty custom bumpers add?
Heavy-duty custom bumpers vary in weight depending on materials and design. Steel bumpers typically add 150-400 pounds, while aluminum options are approximately 30-40% lighter, adding 100-250 pounds. While this does slightly increase fuel consumption, the trade-off in protection is generally worthwhile. Some modern designs utilize high-strength steel and weight-saving techniques to minimize weight gain without sacrificing strength.
Q3: Will installing a custom bumper void my truck warranty?
Installing a custom bumper typically does not void your entire truck warranty. Under the Magnuson-Moss Warranty Act, manufacturers cannot void warranties simply because aftermarket parts are installed. However, if a custom bumper directly causes a specific component failure, that component’s warranty may be affected. Best practice is to choose bumpers produced by reputable manufacturers who offer their own warranties and have them professionally installed by experienced technicians.
Q4: How do custom bumpers affect fuel efficiency?
Custom bumpers’ impact on fuel efficiency depends on design and materials. Traditional flat-plate steel bumpers may reduce fuel efficiency by 1-3%, while aerodynamic designs can minimize this impact. Aluminum bumpers have less effect on fuel efficiency due to their lighter weight. Some modern custom bumpers actually improve aerodynamic performance by enhancing airflow and reducing turbulence, which can offset some of the weight-related efficiency loss.
Q5: What is the average lifespan of a custom semi truck bumper?
Quality custom semi truck bumpers typically last 8-15 years, depending on materials, operating conditions, and maintenance. Steel bumpers offer structural durability but may require rust prevention maintenance; aluminum bumpers provide excellent corrosion resistance and generally require minimal special maintenance. Regular inspection of mounting points, welds, and surface coatings can significantly extend service life. Vehicles operating in extreme conditions may require more frequent inspection and maintenance to achieve optimal lifespan.